The last five years have brought unprecedented challenges to the global supply chain, and the AVL industry has felt the full force of these disruptions. What began as a strain on manufacturing processes quickly snowballed into raw material shortages, labor constraints, and an overwhelming spike in demand. From the COVID-19 pandemic to geopolitical conflicts and shifts in consumer behavior, the ripple effects have reshaped how AVL manufacturers and integrators operate.
Now, as we enter 2024, the question remains: Where do we stand today? And, more importantly, how can businesses and clients adapt to this evolving landscape?
A Recap of the Last Five Years
The supply chain challenges of the past half-decade stem from a convergence of global events. The pandemic triggered shutdowns in manufacturing, transportation, and logistics, halting production and disrupting delivery schedules worldwide. Critical components like microchips—a lifeline for AVL equipment—became nearly impossible to source as production slowed and demand skyrocketed.
For the AVL industry, the situation was compounded by material shortages, including steel, lumber, and plastics, as well as rising freight costs. Labor shortages further exacerbated delays as technicians, engineers, and installers left the industry in record numbers during the pandemic.
Adding to the strain, AVL equipment demand surged as businesses and churches pivoted to virtual solutions during the pandemic, creating unprecedented demand for cameras, audio systems, and streaming technology. Simultaneously, the live event industry experienced a historic surge in touring activity post-pandemic, as artists sought to return to the road after prolonged shutdowns.
These factors created a perfect storm, resulting in long lead times, unpredictable availability, and frequent price increases. Some AVL products faced delays of up to 12-16 months, forcing manufacturers and integrators alike to adapt quickly to a new normal.
Progress Over the Last Two Years
While the supply chain remains strained, the last two years have brought gradual improvements. Lead times, while still extended in many cases, are far more manageable than during the height of the pandemic. Manufacturers have optimized their production schedules and refined their processes to better align with demand.
However, some changes implemented during the pandemic have become long-term adjustments. Many manufacturers have moved away from maintaining extensive “on-demand” inventory. Pre-pandemic, AVL equipment was often readily available, with stock maintained for immediate delivery. Today, lead times of several weeks or even months are more common, with manufacturers shifting to a just-in-time production model.
This shift reflects both production realities and client behavior. Certain segments of the industry, particularly those dealing with specialized equipment, continue to face lead times of three to six months. In many cases, manufacturers have found that clients are willing to work within these timelines, reducing the incentive to return to pre-pandemic delivery speeds.
Managing Client Expectations
One of the biggest challenges for the AVL industry today is managing client expectations. While lead times have improved, many clients assume the supply chain has fully recovered and expect pre-pandemic turnaround times for AVL projects.
This can lead to issues in project planning, particularly when clients wait too long to begin discussions or underestimate the time required for design, procurement, and installation. Without a clear understanding of current supply chain realities, clients risk delaying critical projects or missing key deadlines.
To avoid these pitfalls, clients must approach AVL projects with a proactive mindset. Open communication with a design-build partner is essential to setting realistic expectations and ensuring project timelines align with availability.
Planning for Success
The key to navigating today’s supply chain challenges lies in collaboration and early planning. Clients should involve their AVL partner as soon as possible when considering a new project. An experienced partner can provide insights into lead times, help prioritize equipment needs, and recommend alternatives when availability becomes an issue.
Proactive planning ensures that potential delays are identified early and mitigated before they impact the overall project timeline. It also allows for flexibility in product selection, balancing functionality and availability to achieve the desired outcomes without unnecessary delays.
Looking Ahead
While the supply chain has shown resilience, challenges persist. Some manufacturers face ongoing limitations in production capacity, and global events continue to impact material availability. However, the industry has also adapted, finding innovative solutions and improving processes to meet client needs in this evolving landscape.
For clients and businesses, the takeaway is clear: Planning and partnership are more critical than ever. By understanding current realities and working closely with a trusted AVL partner, organizations can successfully navigate the supply chain and bring their projects to life.
At CTS AVL, we are committed to providing clear communication, proactive solutions, and high-quality results. If you’re considering an AVL project in 2024 or beyond, let’s start the conversation today to ensure your vision becomes a reality.
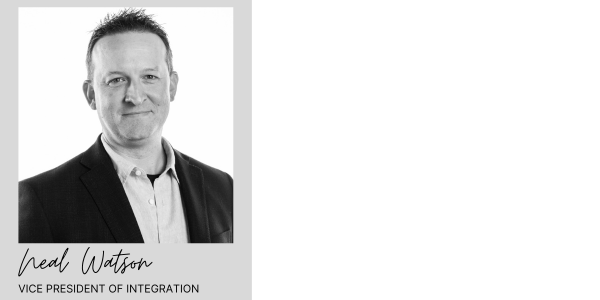